Below, we aim to break down the parts of unspun. Our custom-fit jeans versus our 3D weaving technology. TLDR: custom-fit is our case study of on-demand apparel production and 3D weaving is our game plan to help the rest of the industry get there too.
First things first, our custom-fit jeans are not made with 3D weaving technology.
Our jeans are made to fit each customer's unique body shape and size. The technology we developed and use to make our jeans custom-fit is basically custom-fit patterning software. The jeans are assembled via a relatively normal cut and sew method. We built this custom-fit patterning engine to make the best damn jeans in the world, and (among many other things) to prove that a zero-inventory business model works.
The custom-fit denim process is as follows:
You select your preferred denim cut and color from our website (or app). You also select your waist rise, hem length, and thread color, and then you check-out 💸 .
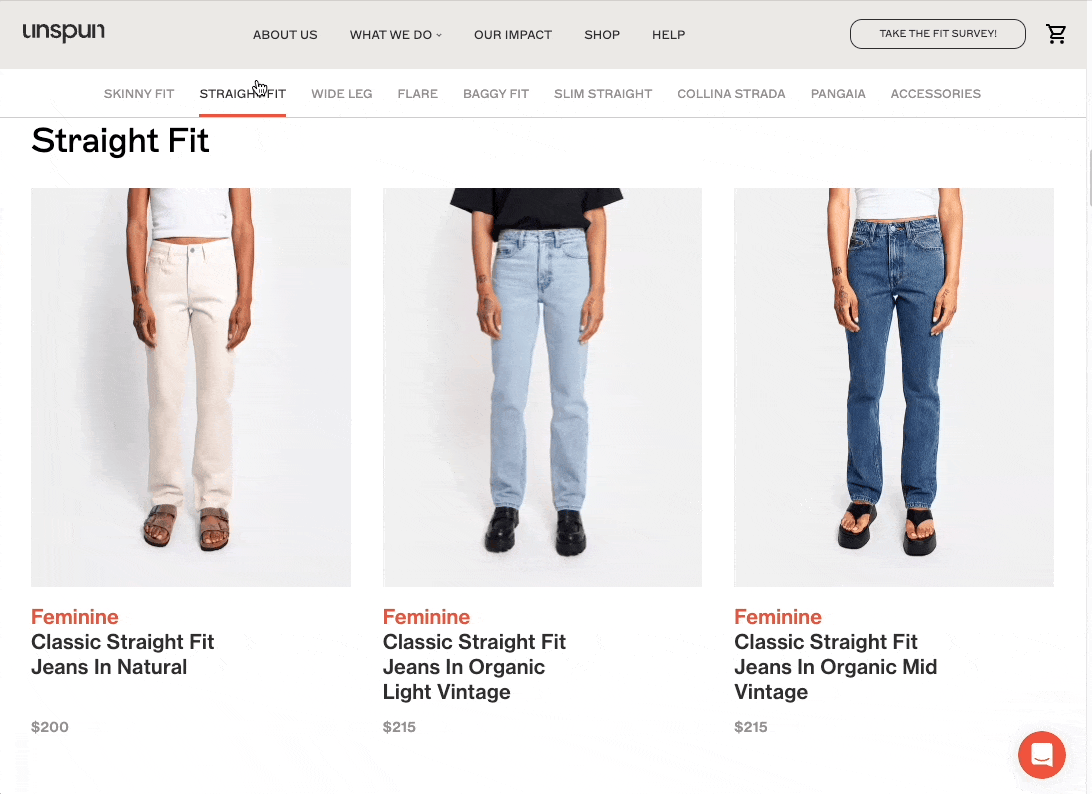
After you’ve checked out (or before, whatever you prefer), download our iPhone app and do a quick 3D body scan and a fit survey.
From there, our tech will connect your 3D body scan data to the fit you selected and generate an individualized set of patterns based on your specs - this is the secret sauce!
We then digitally QC the fit, and send the patterns to one of our partner factories. They do the cutting and sewing of your one-of-a-kind jeans and ship them directly to your home.
As you can see, our custom-fit patterning software thus powers the entire system for our made-to-fit denim production. This method of on-demand production incurs fewer returns, less waste, and ensures we never have any unsold inventory. Boom 💣
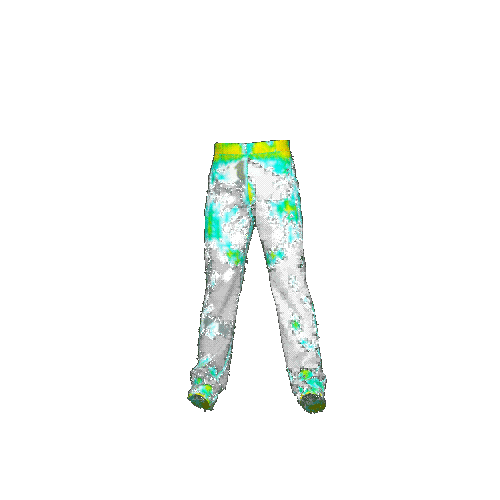
Wait, but what is the Vega™ 3D weaving technology for?
We are building Vega™ 3D weaving technology to weave 3D shapes for clothing. This technology enables us to create clothing quickly and efficiently, directly from yarn.
And by quickly and efficiently, we mean 30x faster than the average industry lead time of 6 months.
By skipping the dyeing, spreading, cutting, and sewing (well, mostly) of garments, Vega™ has the potential to save all the emissions usually generated in these steps of the supply chain.
Vega eliminates the need for large order quantities and inventory, reduces lead times, transportation emissions, and enables on-demand, zero-inventory production. I mean, it’s magical.
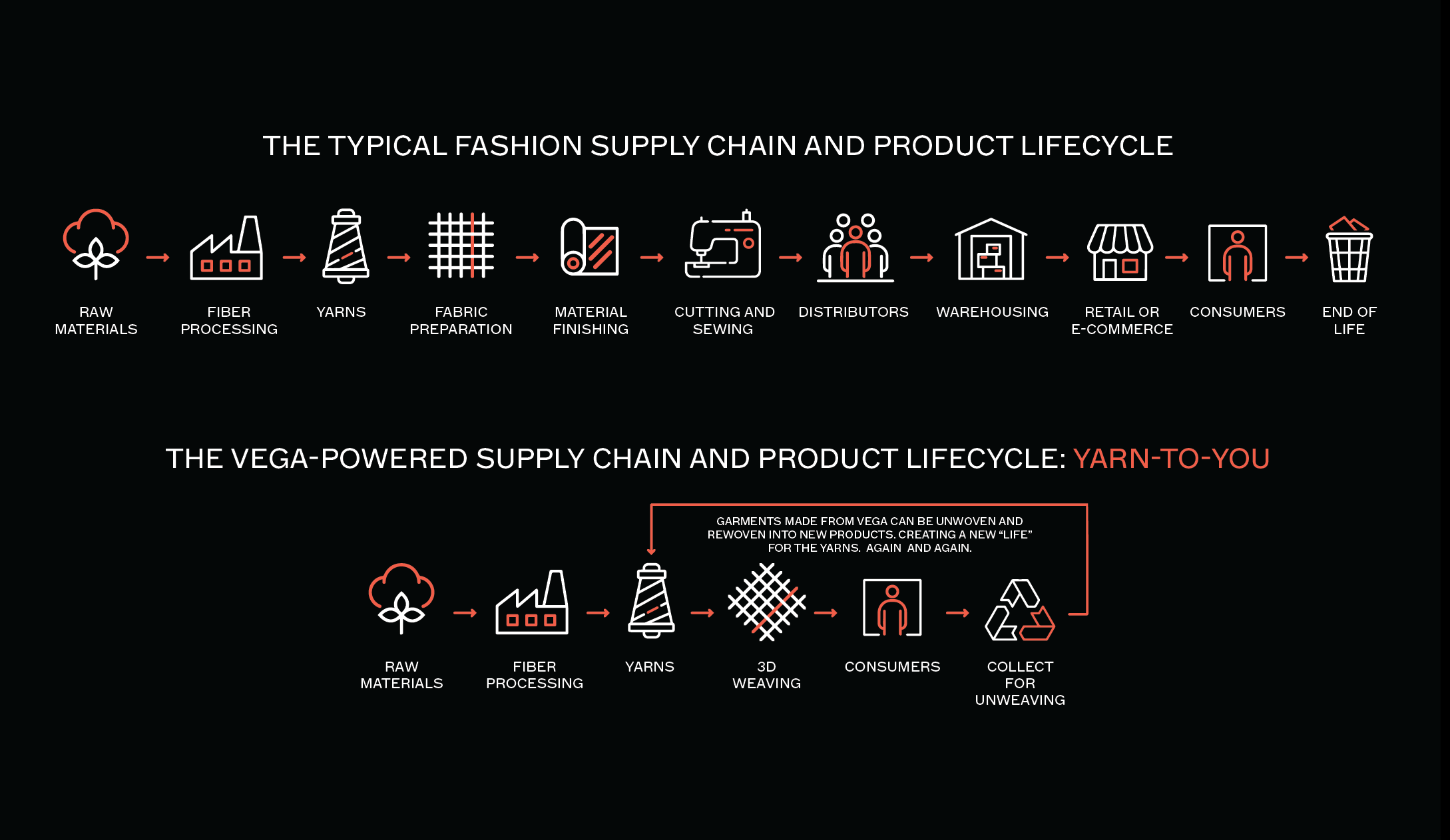
What distinguishes unspun's custom-fit jeans technology from Vega™ technology?
Our custom-fit technology generates individualized patterns for made-to-fit jeans.
The focus is on using software to create better-fitting and completely size-inclusive clothing while reducing waste and overproduction.
Vega™, on the other hand, is a physical weaving machine that uses a set of hardware and software tools to create seamless 3D clothing directly from yarn, eliminating the need for large order quantities and inventory.
So what’s the big idea?
Well, the big idea is to decarbonize fashion supply chains, which, unnecessarily contribute (by some estimates), 10% of global human carbon emissions).
The plan is to deploy Vega 3D weaving machines, in microfactories, around the world. This will allow brands to produce clothing closer to their customers, faster and in lower quantities than current global supply chains will allow, all the while reducing carbon emissions from product transport. Just like our denim, this approach also solves the problem of overproduction.
Short-term, we’ve built the first Vega microfactory right here in Oakland – which also serves as unspun’s new HQ. Our very first brand partnerships will be produced in this facility.
Long-term, we envision localizing these 3D weaving microfactories essentially anywhere there is existing delivery infrastructure – just outside large cities and within range of next-day delivery (ie, no international shipping or cross-country trucking required). A key advantage of a simplified, automated, and localized manufacturing process like Vega is that products for NYC can be made in NYC. Additionally, the small footprint of these all-in-one Vega microfactories can easily fit into existing commercial warehouses.
Our custom-fit software will eventually plug into Vega™, which will, in turn, weave custom-fitted clothing for end consumers. We call it ‘yarn-to-you’.
Although it may sound like a cool "sci-fi solution for the future", it is not. These solutions already exist and represent our proposal for decarbonizing fashion supply chains. We are all living through a climate crisis, and both of these innovative solutions can contribute to a more sustainable future for the fashion industry. We’re ready, are you?
%20small.gif)