Last year, unspun introduced 3D weaving technology to the world. Now, we’re ready to deploy it so fashion can be sustainable at scale.
It’s go time.
Today, unspun announced $32M in a series B fundraising round from the pioneer deep tech firm DCVC, with ongoing backing from Lowercarbon Capital, Decathlon, E12, and SOSV. This investment empowers us to build more Vega™ 3D weaving machines in collaboration with apparel manufacturers and fashion brands to reduce the environmental harms of making clothes while lowering production costs.
What adopting Vega™ can do for the fashion industry
The benefits of 3D weaving are comprehensive. Using a Vega™ machine automates and speeds up apparel manufacturing using less energy than conventional methods. This streamlined production shortens the fashion supply chain, enabling a just-in-time business model that doesn’t require large inventories. The compact supply chain in turn improves the traceability of materials, creates new opportunities for nearshore and onshore manufacturing, and still keeps clothing affordable.
We’re eager for the fashion industry to realize these benefits rapidly. That’s why we’ve designed 3D weaving to be easily adoptable. By licensing Vega™ machines, apparel manufacturers and fashion brands may quickly introduce 3D woven clothes into their product lines while vertically integrating production.
And it’s possible to adopt 3D weaving technology right now. Our series B funding gives us the resources to scale Vega™ manufacturing in hubs strategically located near high revenue markets and to partner with more businesses in the fashion industry. Indeed, we’re off to the races
In Europe, we’re teaming up with an industrial partner to produce 3D woven clothing for multiple fashion brands based on the Continent. (More details forthcoming.) At the same time, we’re adamantly pursuing our initiative to operationalize 350 plus Vega™ machines across North America, with a production capacity of 10 million garments per year, by 2030.
A number of companies have already begun leveraging our technology to gain competitive edge. In March of this year, we announced a landmark project with Walmart to explore manufacturing chinos in-house with Vega™ machines. This effort promises to simplify the omnichannel retailer’s supply chain, fulfill its environmental targets, and onshore its production simultaneously.
We also recently released limited collections of 3D woven pants with the fashion house Eckhaus Latta and the lifestyle brand Teget. Each label used the design interface and jacquard capabilities of our Vega™ machines to test the expressive limits of 3D weaving, as seen in the garments available in our Shop.
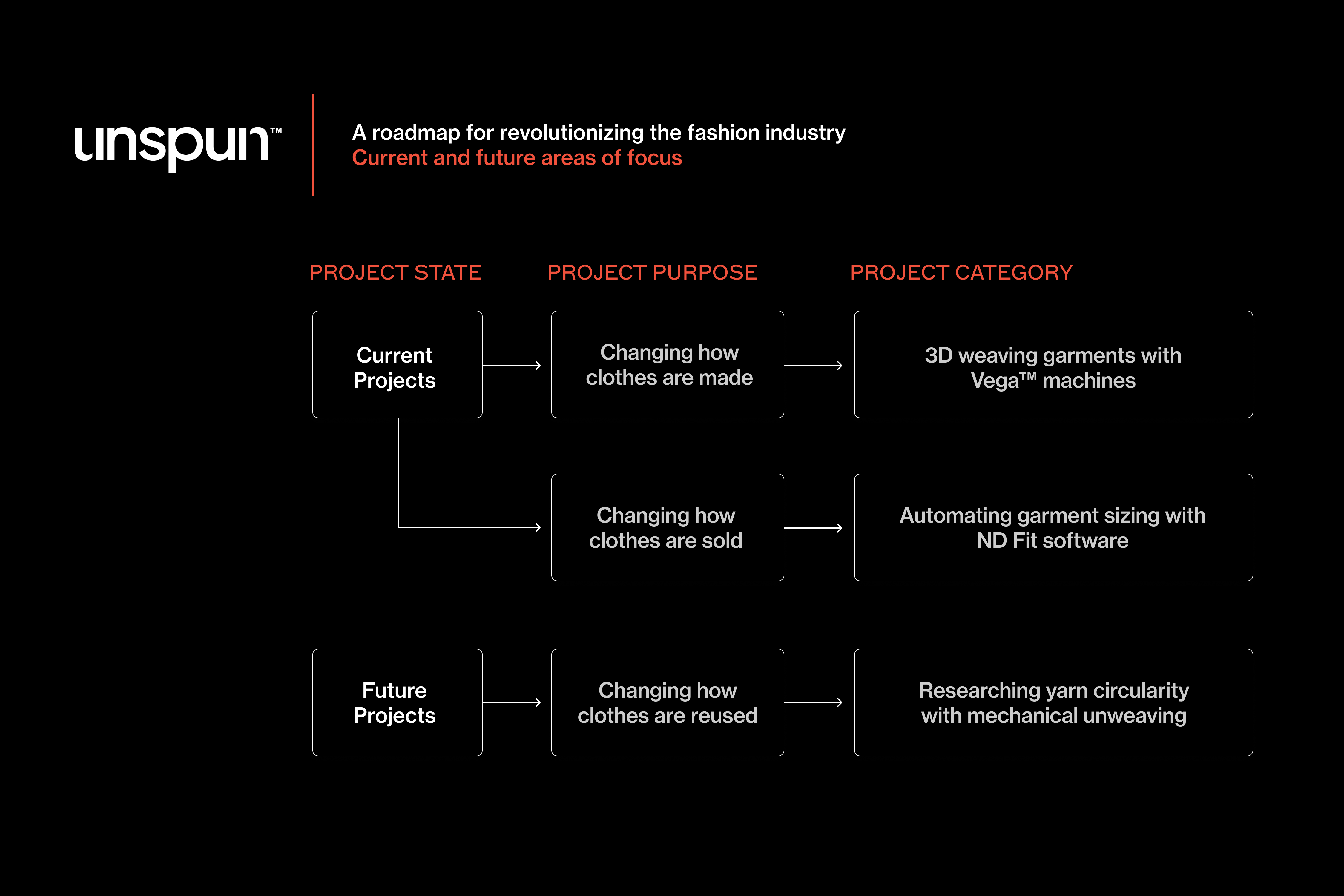
How additional tech can supplement Vega™ manufacturing
These early projects make us confident that Vega™ machines will change how we make and distribute clothing for the better. But we’re equally interested in changing how clothing is sold and disposed of. Not content with curbing waste during production, we likewise strive to prevent clothes from becoming waste after they’re purchased
This fundraising round allows us to advance the work we’ve undertaken to minimize return rates. Separate from our pursuit of 3D weaving, we’ve made thousands of bespoke jeans for direct consumers with diverse body types. This experience has informed the development of our ND Fit engine, an automated size recommendation and patternmaking algorithm.
In the near future, ND Fit can increase the likelihood that any cut-and-sewn garment a customer buys will fit them well. Long term, ND Fit can augment the fits of 3D woven garments by connecting to our Vega™ design interface.
This round helps us continue researching circular solutions for the clothes we make as well. Here, we’re focused on the prospect of recapturing yarns from old 3D woven garments by mechanically unweaving them, and using those yarns to make new garments. Although a theoretical technology, unweaving may have profound ramifications. If perfected, it could decrease the amount of virgin material needed for manufacturing, without requiring that existing fabric be recycled.
Why the time to use Vega™ is now
Making apparel production more efficient with 3D weaving technology. Lowering returns. Achieving circularity. Decreasing human global carbon emissions by 1%. Does this sound a little ambitious?
We don’t think so. And our investors don’t think so either.
The precarious state of our planet calls for big solutions. unspun’s Vega™ machines and associated software answer that call.
In 2024, the fashion industry must contend with market pressures, supply chain bottlenecks, and increasing regulation spurred by climate change. The industry can no longer afford to entertain the notion that fixing the problem of clothing waste will come at the expense of profits.
For manufacturers and brands that adapt to this moment, the opposite will prove true. In DCVC partner Rachel Slaybaugh’s words, “it’s good business to align profits and climate impact.”
We’re proud to have received affirmation from top tier climate investment firms that our technologies have the power to be as broadly effective as we envisioned them. Now is our time to demonstrate that effectiveness.
No time like the present. Read more about our Series B funding in this Fast Company article.